Newly developed RTM press system to revolutionize aerospace manufacturing
Langzauner has achieved a breakthrough in aerospace manufacturing technology through its collaboration with the University of Sheffield Advanced Manufacturing Research Centre (AMRC).
Posted On 04 Mar 2025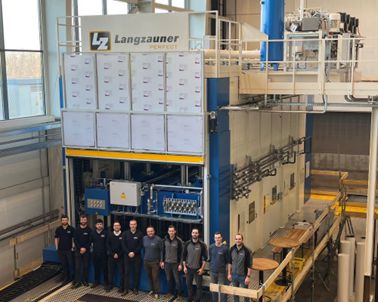
Langzauner (Austria), a pioneer in advanced hydraulic press systems, announced that it has achieved a breakthrough in aerospace manufacturing technology through its collaboration with the University of Sheffield Advanced Manufacturing Research Centre (AMRC).
AMRC’s Composites at Speed and Scale (COMPASS) is a major boost to aerospace research and development in the UK with a new, open access innovation facility which will initially house industry leader Boeing’s research project to de-risk and develop high-rate sustainable structures.
At the heart of this innovation is Langzauner’s newly developed Resin Transfer Moulding (RTM) press system, the largest of its kind globally for integral aerostructural parts. Using this state-of-the-art press system, the project aims to reduce large component process times by a factor of ten – from approximately 40 hours to just four hours – while maintaining exceptional quality standards.
“This technology represents a quantum leap in aerospace manufacturing capabilities,” said Alexander Wiesner, Head of Global Sales & Marketing of Langzauner. “We’re not just building equipment; we’re revolutionizing how the next generation of aircraft will be produced.”
The press system features an impressive 10,500mm x 3,500mm platen size and delivers unprecedented precision with fully adjustable pressing force up to 2,400 tons.
The system’s revolutionary features include:
- Extraordinary press force regulation accuracy of 0.1%
- Advanced sliding table system accommodating 180-ton mould mass
- Sophisticated plate parallelism control within hundredths of a millimeter
- Individual cylinder control with active parallelism management
- Innovative gap injection functionality with two-axis rotation capability
The system is fully integrated with IIoT capabilities, enabling comprehensive data collection for artificial intelligence and machine learning applications in factory-scale process optimization.
Darren Wells, Senior Technical Fellow for Large Composite Structures at the AMRC, said: “When we created the specification for such a groundbreaking piece of equipment, we knew we had set the bar very high in what was achievable.
Langzauner’s solution not only meets all of our targets, but exceeds in many of them meaning this press will be at the forefront of high-rate composite manufacturing research for years to come.
Langzauner’s commitment to vertical integration is further demonstrated by the ongoing assembly of a large-scale Hot Drape Former for RTM preform preparation, ensuring a complete solution for next-generation aerospace manufacturing needs.”
This development positions Langzauner at the forefront of aerospace manufacturing technology, supporting the industry’s push toward more efficient, sustainable, and scalable production methods for future aircraft generations.
Realted Content
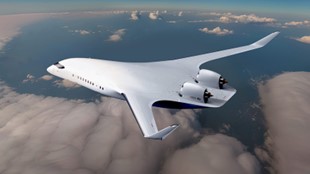
Siemens unveils breakthrough innovations in ind ...
Siemens showcased its vision for the ...
Read More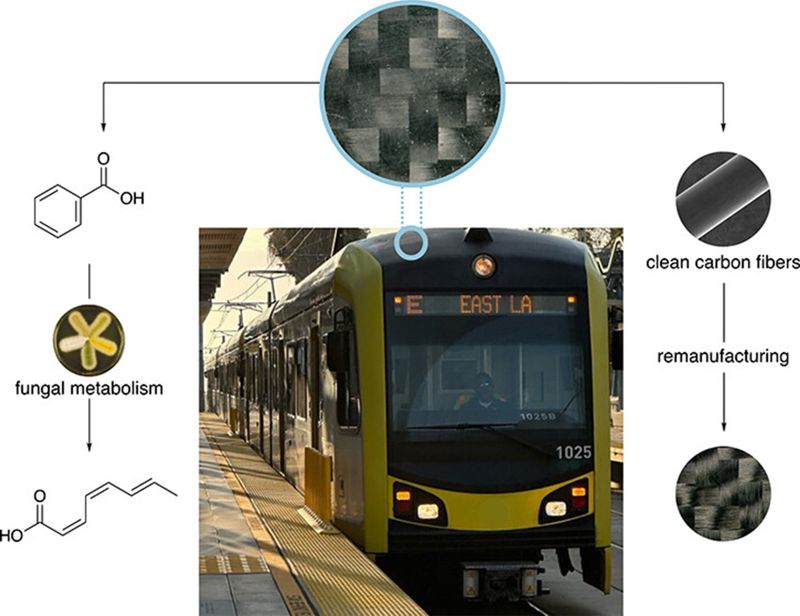
Researchers develop a biotechnological process ...
Researchers have developed a chemical ...
Read More