Helicopter door design with advanced materials and manufacturing processes
At the heart of the project lies the development of Sheet-Molding-Veil (SMV), a next-generation composite material designed to replace traditional Sheet-Molding Compounds (SMC)
Posted On 27 Feb 2025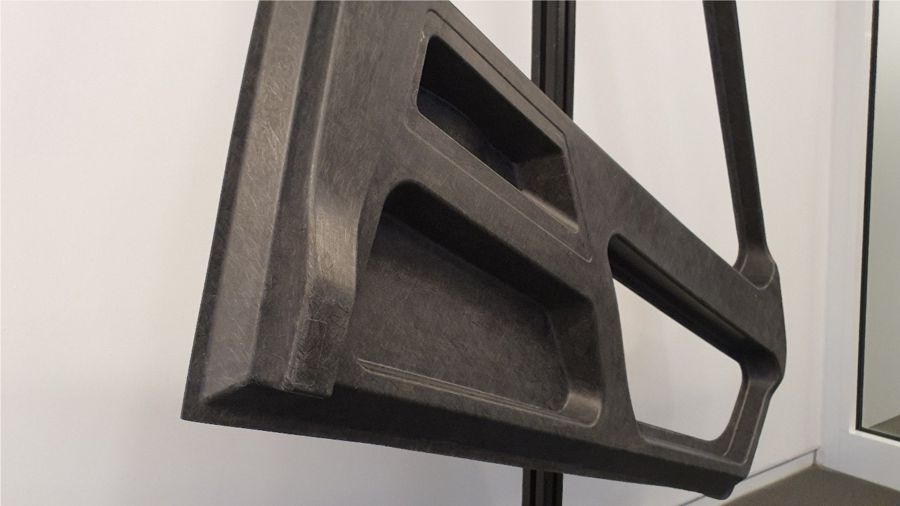
The aerospace industry is on the brink of a major innovation with the development of a new generation of helicopter doors. Combining cutting-edge material science with advanced manufacturing techniques, this project has achieved a breakthrough in the design and production of lightweight, high-performance inner door shells. The result is a sustainable, efficient, and adaptable solution tailored to meet the challenges of modern aviation.
This initiative focuses on creating thin-walled, complexly shaped door shells with a thickness of just 1.2 mm. Developed by Fraunhofer IGCV in Augsburg, the process employs wetlaid nonwoven materials, consisting of a carbon fiber / thermoplastic fiber-blend, enhanced for superior performance and drapability. The reinforcement material is further processed using a state-of-the-art vario-thermal pressing cycle carried out at the DLR Center for Lightweight-Production-Technology (ZLP) in Augsburg. Together, these advancements demonstrate the feasibility for large-scale industrial application.
This project is a collaborative subsequent initiative of Fraunhofer IGCV and German Aerospace Center (DLR)to the joint research project “LIGHT” (grant number: LABAY112), funded by the Bavarian Ministry of Economic Affairs, Regional Development and Energy, where the helicopter door design and the press mold have been developed. Airbus Helicopters in Donauwoerth kindly provided the mold.
Sheet-Molding-Veil (SMV): A Material Innovation
At the heart of the project lies the development of Sheet-Molding-Veil (SMV), a next-generation composite material designed to replace traditional Sheet-Molding Compounds (SMC). SMV features selectively created fiber agglomerates within a nonwoven base material, replicating the structural benefits of SMC while incorporating recycled fibers for enhanced sustainability.
The SMV wetlaid nonwoven, consists of 12 mm-long carbon fibers. It achieves a consolidated ply thickness of 0.2 mm with adjustable fiber volume content between 30 to 42 %. This lightweight yet robust material ensures optimal performance, including isotropic mechanical properties and improved compatibility with thermoset and thermoplastic matrices.
Advanced Processing and Precision Manufacturing
The SMV material is manufactured using a process that combines precision and efficiency. Preforms made from six layers of nonwoven are subjected to a vario-thermal pressing cycle, which involves heating, pressing, and cooling in a custom-designed mold. This process allows the material to conform seamlessly to complex geometries while maintaining uniform quality and high-performance characteristics. The SMV wetlaid nonwoven ensures smooth and consistent shaping during forming, making it an ideal material for intricate aerospace applications like helicopter door components.
Performance, Sustainability, and Versatility
SMV offers a combination of high mechanical performance, sustainability, and functional versatility. By utilizing recycled fibers and enabling full recyclability, it significantly reduces the environmental footprint of aerospace components. The nonwoven base material also provides additional benefits, including noise and vibration insulation, electromagnetic shielding, and improved thermal management.
Engineers have further enhanced the material’s adaptability by enabling customization at the material level. Properties such as fiber blends, additives, and grammage can be fine-tuned to meet specific application requirements, making SMV a versatile solution for diverse industries.
Paving the Way for the Future of Aviation
The collaborative efforts of Fraunhofer IGCV and DLR ZLP in Augsburg have set a new benchmark for aerospace innovation. By combining sustainable materials, advanced manufacturing processes, and exceptional performance characteristics, this project demonstrates a bold vision for the next generation of lightweight, high-performance aerospace components.
Realted Content
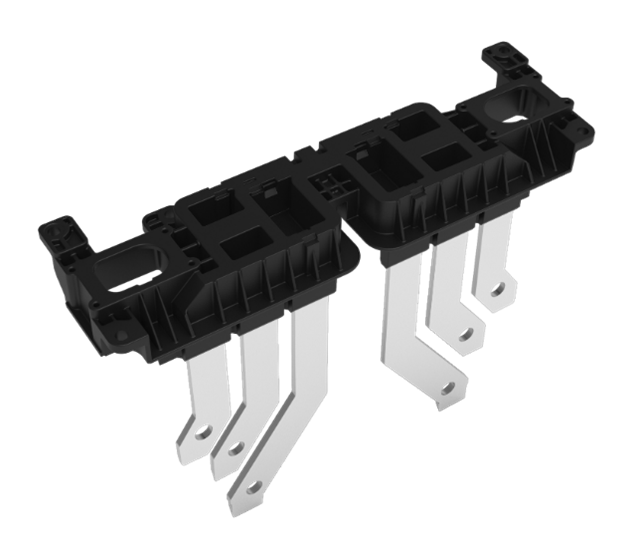
BASF launches innovative PPA for electric vehic ...
BASF announced that its newly develop ...
Read More