Development of composites rotor blades for flying car
PAL-V and Royal NLR have successfully completed the development of the rotor blades for the PAL-V Liberty
Posted On 12 Feb 2025
PAL-V, the leader in FlyDrive mobility solutions announced a significant milestone in their collaboration with Royal NLR - Netherlands Aerospace Centre. The two parties have successfully completed the development of the rotor blades for the PAL-V Liberty, marking the beginning of the industrialization phase. This achievement brings PAL-V another step closer to the serial production of its revolutionary FlyDrive vehicle (flying car).
The design of PAL-V’s rotor blades was undertaken by NLR, Netherlands’ leading aerospace research institute. NLR's extensive experience in aerospace engineering and composites structures has been crucial in refining the design and ensuring it meets the highest standards of performance and safety. The rotor blades are 20% more efficient with less drag compared to equivalent blades, resulting in better performance and fuel economy. Due to the advanced composites technology, a set of two rotor blades only weighs 35.8 kg while spanning over almost 11 meters in length.
PAL-V and NLR have been working closely together to perfect the rotor blades, leading to the current phase where they are ready for mass production. PAL-V has already set-up a small-scale assembly location near its headquarters in the Netherlands, where it is preparing for the serial production of the Liberty.
Henri de Vries, Senior Scientist at NLR said, "Together with PAL-V we’ve overcome technical challenges and ensured our rotor blades are ready for industrial production. Gyroplane rotor blades are brought in motion by the airflow to create lift instead of by using a motor, this is called autorotation. So the PAL-V blades are basically its wings during flight. Next to being lightweight, they contain a mid-hinge to fold the blades and enable driving the vehicle on the road with a convenient vehicle length of just 4 meters. This makes its design unique and unprecedented."
NLR’s state-of-the-art facilities, including wind tunnels, composites manufacturing facilities, structure testing equipment and even a landing strip, have all been used in the R&D and certification testing of various parts and subsystems of the PAL-V Liberty. The partnership with NLR will continue to play a key role as PAL-V approaches the launch of its first production units.
Realted Content
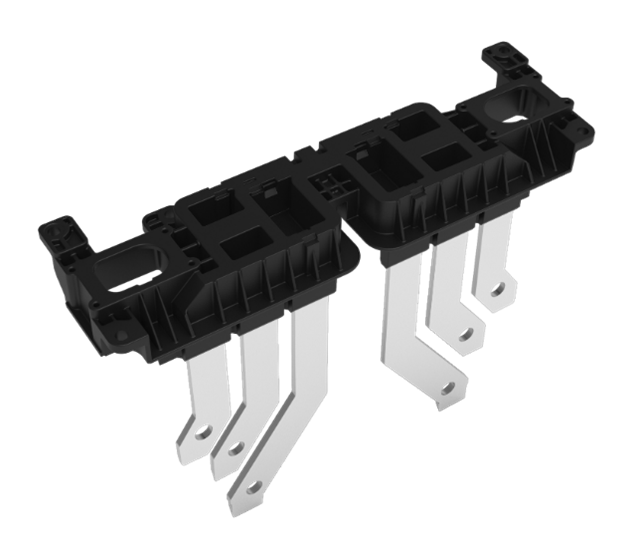
BASF launches innovative PPA for electric vehic ...
BASF announced that its newly develop ...
Read More